Tubing for peristaltic pumps & Life-Sciences
Tubing made of different materials.
Product overview
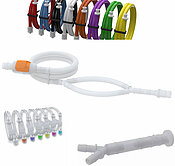
Custom tubing assemblies
- Colored or natural tube options
- Colored Luer connections for line distinction
- Large selection of connectors and quick couplings (no spill)
- LaserWeld™ products available with T-piece, cross and Y-barbed fittings, and mini and 1" flange connectors
- Pre-coiled tubing for space-saving
- Filtration assemblies
- Tubing assemblies for peristaltic pumps
- Laser Clamp® welding technology
- Manufacturing and packaging in a clean room
- Single use and autoclavable
- Individual packaging solutions
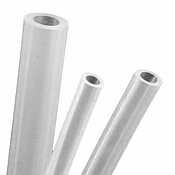
Silicone tubing
Platinum-cured silicone tubing for peristaltic pumps and pinch valves.
Also in biocompatible version.
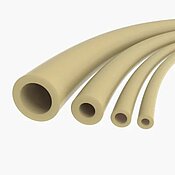
EJ Prene™ Tubing
- Outstanding performance when used in peristaltic pumps
- Precise flow rate
- High chemical resistance
- Sterilizable (autoclave, EtO sterilization, gamma sterilization 45 kGy, withstands multiple autoclaving cycles)
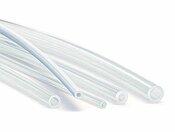
PTFE Tubing
- Continuous operating temperature: -100 - 150°C
- Good optical clarity (96% UV transmission)
- Very smooth internal surfaces
- Excellent chemical resistance
- Tight dimensional tolerances
- Biocompatible
- FDA & USP Class VI compliant
- Gamma & ETO sterilizable
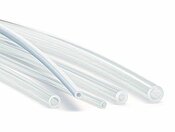
FEP Tubing
- Continuous operating temperature: -51 - 50°C
- Good optical clarity (96% UV transmission)
- Very smooth internal surfaces
- Excellent chemical resistance
- Tight dimensional tolerances
- Biocompatible
- FDA & USP Class VI compliant
- Gamma & ETO sterilizable
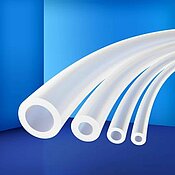
TPE 121 Tubing with Shore-A 54
This tubing series made of the material TPE was specially developed for the usage in peristaltic pumps and pinch valves.
USP Class VI approval, production in clean room according to ISO 10993-5 and ISO 10993-4 standard.
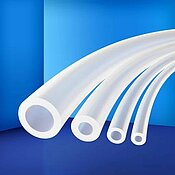
TPE 135 Tubing with Shore-A 68
This tubing series made of the material TPE was specially developed for the usage in peristaltic pumps.
USP Class VI approval, production in clean room according to ISO 10993-5 and ISO 10993-4 standard.
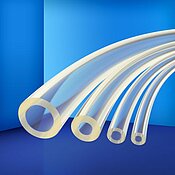
Flexible Kynar®-PVDF Tubing
Due to the inner coating with PVDF, this tubing is highly chemical resistant, but remains flexible due to the outer tube material TPU. This enables the use of barbed-connectors, which allows the easily, quickly and cost-effectively implementation of fluidic paths in devices compared to 100% PTFE tubing.
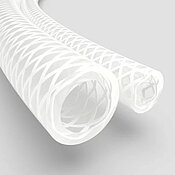
Braided Reinforced TPE-Tubing
Alternative to silicone tubing for high purity fluid under pressure with biocompatibility for demanding biomedical and pharmaceutical applications.
Sterilization stability of materials of tube materials
Please note the disclaimer of liability*
Material
|
Gamma Radiation
|
Ethylene Oxid
|
Autoclave
|
---|---|---|---|
Polyurethane
|
Excellent. Some discoloration may occur, but reverses over time. No significant effect on physical properties.
|
Excellent. No noticeable effect on material properties.
|
Not Recommended. Hydrolysis of polyurethane may create aromatic amine impurities.
|
Polyethylene
|
Excellent. Tensile strength increases and modulus of elasticity decreases due to cross-linking of polymer.
|
Excellent
|
Not Recommended. Tubing may distort at common autoclave temperatures.
|
Kynar
|
Highly compatible, but will discolor to brownish hue. Physical Properties typically improve.
|
Excellent
|
Excellent
|
*The data presented in this publication is for reference only. It was compiled primarily from outside sources provided by feedstock materials suppliers and resin manufacturers, and is offered to our customers as a means of comparing the characteristics of resins and materials used by us at the time of publication. The particular conditions of your use and application of our products are beyond our control. Thus, it is imperative that you test our products in your specific application to determine their ultimate suitability. All information is provided without implied or expressed warranty or guarantee by us, or the resin and feedstock manufacturers. We assume no liability with respect to the accuracy or completeness of the information contained herein and none of the information provided constitutes a recommendation or endorsement of any kind by us.